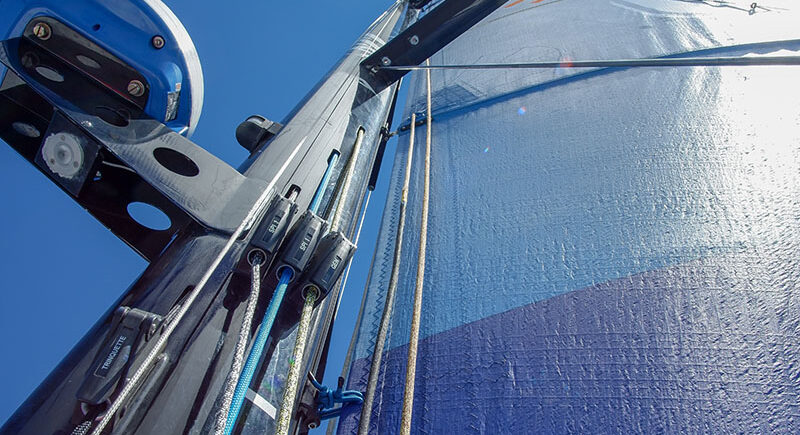
GUIDE D’ACHAT
1/3 Cable standing rigging | The different technologies of textile cable standing rigging
Textile cable is the association of a material (aramids, PBO, carbon, Dyneema) with a construction technique (filament winding, pultruded UD, braiding). Each solution is relevant to a type of sailboat and its programme (offshore racing, coastal regatta, open sea cruising, fast cruising, and so on). To help you synthesise and choose the most adapted textile standing rigging technology, we have compiled the main data in a table. Who do you say thanks to? (silence!)
Filament winding
Filament winding consists in winding unidirectional (non-braided) fibres around two thimbles. This is the oldest solution in the history of modern ropework to create textile standing rigging. Oldest doesn’t mean old fashioned! Currently, it is still the most efficient technology as it combines stability (the fibres are in the direction of the strain) and lightness (the thimbles take on very little load and are thus light). The fibres are surrounded by adhesive tape that compacts them and creates a protective first layer.
The cable is then covered (Dyneema cover most of the time) to avoid chafing.
Filament winding is a technology that requires a lot of workforce, which makes it expensive. There are industrialised processes. Fibremax, in the Netherlands, is currently developing a robot project to make filament winding over 7 km, to create textile cables for cranes, bridges, offshore platforms… A whole new world!
+stable
+light
-expensive
Extruded / pultruded UD
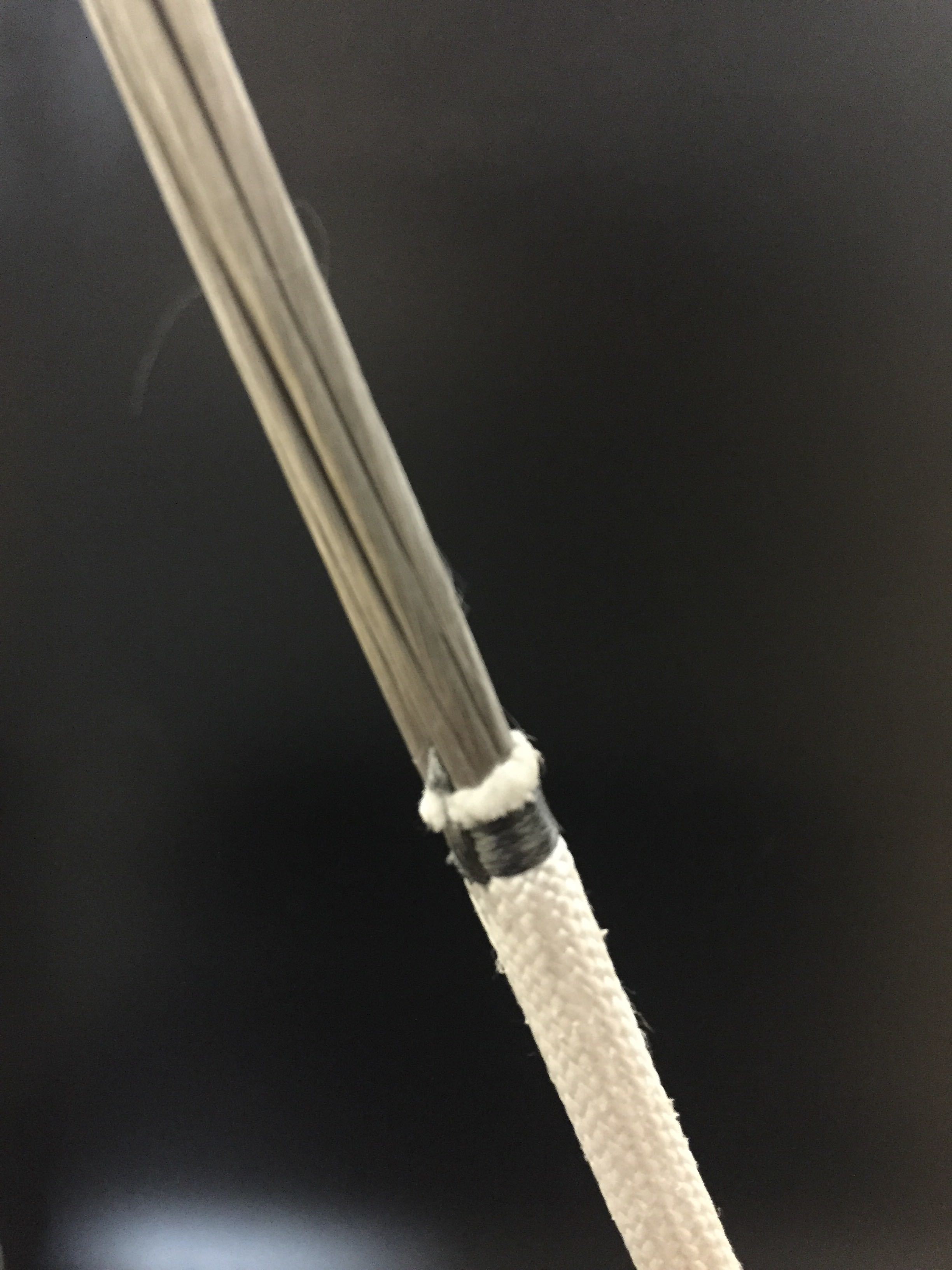
Despite its unappealing name, this is the most widespread solution. This technology is used to build shrouds in Kevlar ® and PBO. Since they aren’t twisted, the unidirectional fibres (UD) must be stuck together at each end. The endings also contribute to blocking the fibres (in case of bi-conic ends, the tightening of the two interlocking cones increases with the tension). The fibres are protected by an extruded plastic (like electric cables). Standing rigging in pultruded UD is more affordable than filament winding because its installation is simpler. This is an efficient solution as it is very stable (UD fibres in the direction of the effort) but its weight is its weakness. The cover and endings make it much heavier, which is particularly advantageous on discontinuous rigging where there are many endings.
+stable
+more affordable than filament winding
-heavier than filament winding and braiding
Braided textile cables
Among the fabrication techniques of textile cables, braiding is the third type we come across. Braiding is less stable than filament winding or pultruded UD: the fibres make an “S” and aren’t directed in the exact direction of the effort. Braiding implies certain elasticity, even if the fabrication techniques tend to minimise it. A very long braid pitch reduces elongation (the S curve is highly reduced). Heat pre-stretching (tensioning the braid at its working load) also stabilises it.
But why make braided textile cables when filament winding and pultruded UD offer great stiffness? Braiding is easy to install, and so much more affordable! Bluewave is developing an entire range of ending solutions, which also makes things easier. Braiding is a reliable technique since the rope doesn’t need to be protected by a cover (except on the major wear areas like front sail sheets for instance). This is the case of Dyneema®, highly resistant to UV and chafing.
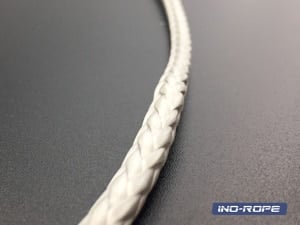
Due to the issues of elongation caused by braiding, a Dyneema® braided textile standing rigging isn’t relevant for boats seeking extreme rigidity. But it is a relevant solution for “small” racing units (up to 40 feet) or cruising sailing boats, as it combines efficiency and lightness. For this type of vessel, Dyneema® shrouds are considerably lighter than pultruded UD. On board a Melge 32, textile standing rigging in pultruded UD weighs 5 kg versus 3.5 kg in Dyneema® braid, which saves 30% of weight.
+ most affordable solution
+ lighter solution than pultruded UD
– elongation due to braiding
-
⌀ de 2 à 10 mmDyneema SK99 braid1,18 € – 18,40 € TTC
-
Special rope scissors (Dyneema®, Kevlar®)44,90 € – 49,90 € TTC
-
⌀ de 7 à 12 mmRope to splice, SK99 Dyneema® core, SK78 Dyneema® cover9,30 € – 24,18 € TTC
-
⌀ de 2 à 10 mmRope with low elongation (runners, shrouds, strops…) | 100% Dyneema®0,82 € – 20,60 € TTC